PM, PDM, RTF, THIS, THAT, THE OTHER
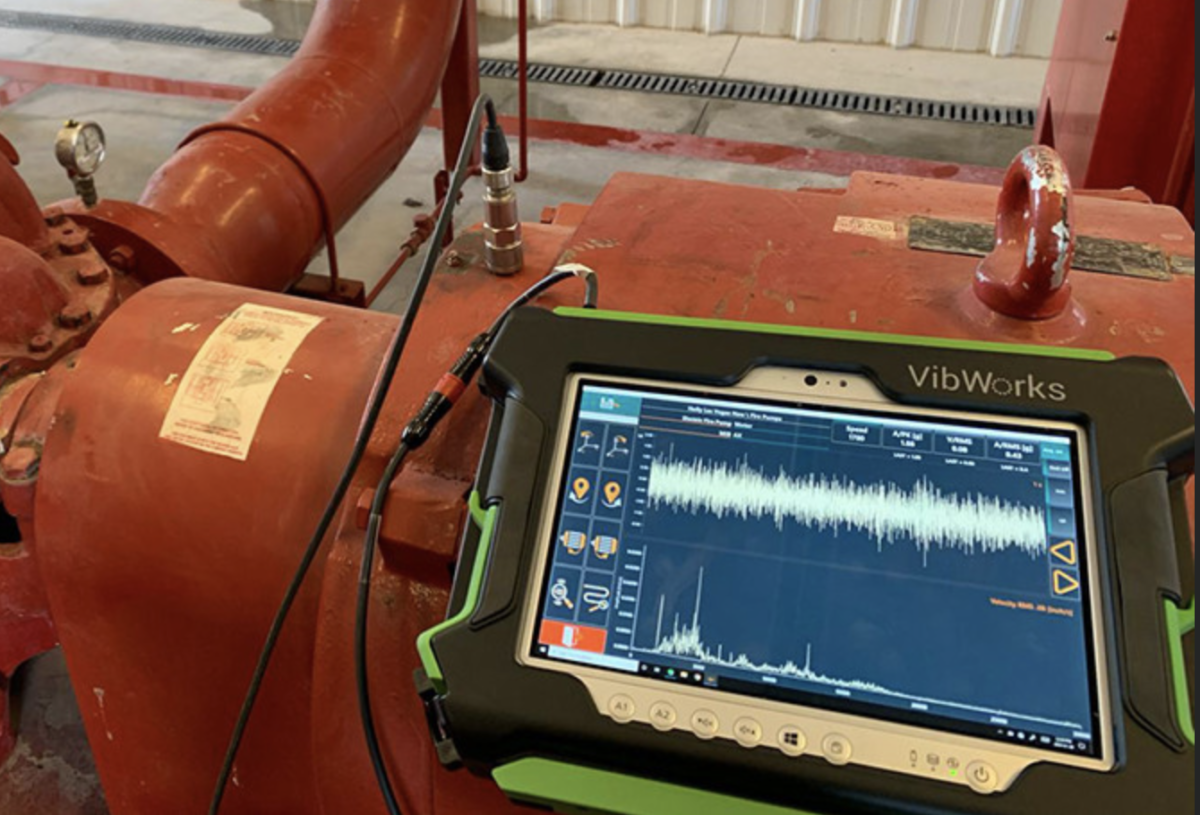
In the last few decades, we have heard many companies perform “PMs” (Preventive Maintenance tasks) on their assets or buy tools to help perform “PdM” (Predictive Maintenance), often hoping to solve all their problems without a real strategy in place. This can be a costly mistake as it risks inducing functional failures in your assets during their infant mortality period as a result of performing unnecessary intrusive work. There are many different maintenance strategies, which are essential for ensuring the reliability and availability of equipment and assets. However, companies should not just arbitrarily choose one for their maintenance department to follow. Instead, the maintenance strategy should fit what is best for a given asset. The most common strategies are Preventive, Predictive, and Run-to-Failure, although it may initially sound strange. Now, let’s take a look at how they differ.
MAINTENANCE STRATEGIES:
1. PREVENTIVE
A Preventive maintenance strategy is based on performing a maintenance task at periodic intervals. One example of such a strategy is greasing a bearing quarterly, regardless of whether that bearing actually needs greasing at that time. This is a good strategy to use when failures are expected to occur after a certain amount of time or number of hours of operation. We typically use a Preventive maintenance strategy with our vehicles. When we change the engine oil in our car, we typically do so every three to six months or every 3,000 to 10,000 miles. Whatever the chosen interval is, it is based on time or usage. Alternatively, we could periodically take an oil sample and send it to a lab for analysis to get the condition of the oil and trend that condition. This would more accurately tell us when we will need to change the oil. However, this strategy doesn’t make sense because it is not cost-effective. Changing the oil in the car can cost around $50 to $80. Performing an oil analysis just once would cost much more than that. Therefore, it is easier and more cost-effective to get the oil changed periodically to prevent engine failure. It is important to perform a cost analysis for each maintenance task, to determine if it makes more sense to use a preventive or predictive maintenance strategy.
2. PREDICTIVE
A Predictive maintenance strategy is typically used on critical equipment. It is based on Condition Monitoring. Condition Monitoring is a periodic check of the condition of a particular component or asset. Technologies used for Condition Monitoring are Vibration Analysis, Ultrasound Testing, Infrared Inspection, and Oil Analysis. For critical assets, it may not be cost-effective to shut the equipment down for days to do periodic bearing replacements. However, it does make sense to check the condition of the bearing (and trend it over time), so that maintenance can be planned for and executed well before a failure is predicted to occur, thereby minimizing the cost of repair and preventing any potential unplanned downtime or catastrophic failure of the equipment.
3. RTF (RUN-TO-FAILURE)
An “RTF” (Run-To-Failure) strategy, as the name implies, allows an asset to be operated until it fails. The asset is then replaced. Typically, this strategy should only be chosen when the criticality of the equipment is low, and the failed asset or component is quickly, easily, and cheaply replaceable. In these cases, applying a predictive or preventive maintenance strategy may be more costly or inefficient than simply letting the asset fail. Again, careful cost analysis that includes an accounting of all relevant factors such as labor cost, parts costs and downtime/lost production is key to determining successfully which maintenance strategy is best to use for each asset.
Choosing the right maintenance strategy for your equipment is crucial for minimizing downtime, increasing reliability, and maximizing the lifespan of your assets. Preventive, Predictive, and Run-to-Failure strategies each have their benefits and drawbacks, and the decision to use one over the other should be based on careful cost analysis and consideration of the criticality of the equipment. Doing so has shown that it can help drive a reliability program to success.
Article by: Adam Stredel CRL.
Ludeca