IS PULLEY ALIGNMENT IMPORTANT FOR YOU?
Most every running asset – no matter the mechanism used when coupled together – can be subject to misalignment between driver and driven components. Proper alignment of belt-driven equipment is often neglected by maintenance and even reliability departments even though pulley misalignment is a principal reason for reduced belt life, premature sheave wear, and higher than necessary power consumption.
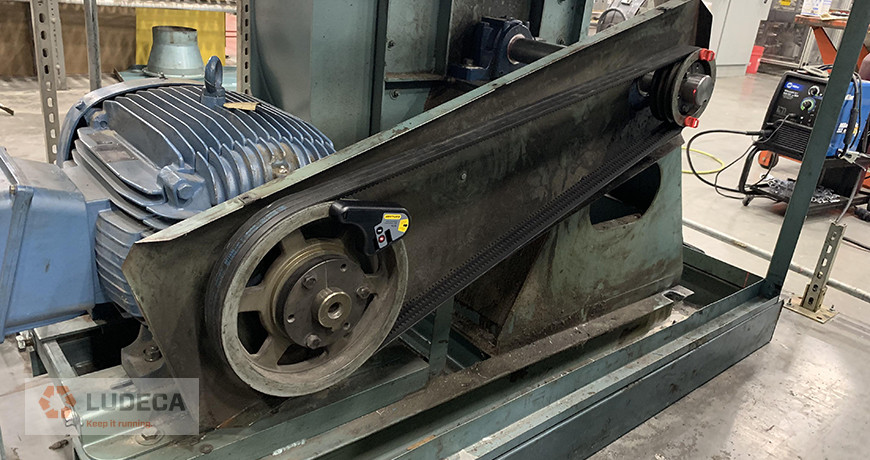
HOW CAN BELT MISALIGNMENT AND ITS DAMAGING CONSEQUENCES BE PREVENTED?
With today’s strict reliability requirements, the best method to utilize for belt alignment is a laser alignment instrument designed for this task. In addition to providing an extremely accurate, cost-effective, and time/labor decreasing process, there is the added bonus that some tools available on the market also offer a detailed report of the work performed, including photos which can be archived for future reference. The Reliability and Maintenance group can easily be trained to incorporate proper belt alignment procedures such as that presented in LUDECA’s 5-Step Sheave/Pulley Alignment Procedure into their maintenance intervals. The ROI with these types of instruments is very quick; this will allow savings and profits to rise almost immediately.
HOW EASILY CAN YOU IMPLEMENT LASER PULLEY ALIGNMENT SYSTEMS DESIGNED FOR BELT APPLICATIONS INTO YOUR RELIABILITY PROGRAM?
Belt alignment systems for this task such as the Dotline Laser, SheaveMaster, or SheaveMaster Greenline laser pulley alignment tools are good. They indicate misalignment in all three degrees of freedom (axial offset, horizontal angularity, and twist angle) instantly. However, systems like the Easy-Laser XT190 take it several steps further as the instrument communicates with either the XT11 tablet or to any smartphone/tablet via Bluetooth with the Easy-Laser XT Application and displays all this information live on a screen as you are performing the corrections. Upon completion, the system provides you with a full report. A maintenance or reliability technician can easily determine and correct belt alignment conditions in a short period of time.
Remember that for any tool you use, always ensure that the mounting surfaces (pulley faces) are free of dirt or rust, and don’t forget to verify the proper tension of the belts has been set after the alignment.
Defects related to belt alignment issues can have a severe impact on the reliability of your assets. Be proactive and take advantage of best-practice belt alignment techniques to increase your uptime and the life of your assets.